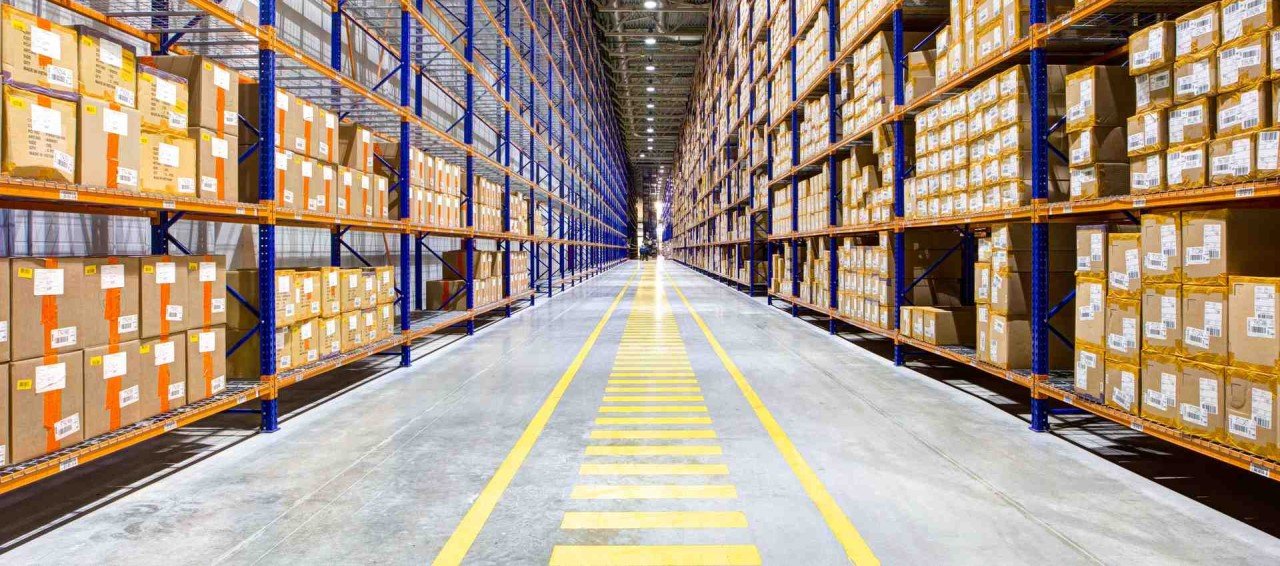
Effective Inventory
Management
Effective inventory management is the backbone of efficient distribution centre (DC) operation.
It ensures that goods are stored, tracked, and dispatched in an organized manner, directly impacting operational efficiency, customer satisfaction, and profitability. However, as the UK logistics industry faces mounting pressures—from the rise of e-commerce with increasing customer expectations for fast, accurate deliveries to the global disruption in supply chains through polarised geopolitics—the challenge of inventory management has never been more complex.
For DC operators, inefficient inventory management can lead to a host of problems, from stockouts and overstocking to increased operational costs and inconsistent order fulfilment. Addressing these challenges requires a deep understanding of the factors that affect inventory control and the implementation of cutting-edge solutions that can streamline operations and drive performance.
There are several challenges regarding ensuring effective inventory management:
1. Increasing E-Commerce Demands
The explosive growth of e-commerce has fundamentally changed the way distribution centres operate. In the past, DCs primarily dealt with large, bulk orders from businesses to businesses (B2B). Today, they handle a vast number of smaller, more complex consumer orders (B2C), often with more frequent and varied product lines. As online shopping has become a daily activity for millions of people, distribution centres must manage larger volumes of stock, deal with more frequent deliveries, and accommodate a greater number of SKUs (stock-keeping units).
This transformation leads to several issues. With an increasing number of SKUs and fluctuating order volumes, it becomes more challenging to forecast demand and ensure that the right products are in stock at the right time. Inefficient inventory management can result in stockouts for popular items or the overstocking of slow-moving products, both of which negatively impact customer satisfaction and operational costs.
2. Supply Chain Disruptions
The global supply chain disruptions triggered by the COVID-19 pandemic, coupled with Brexit-related uncertainties, have had a lasting impact on inventory management in the UK. Add in the additional tariff trade war and it is not surprising we are seeing delays in manufacturing, transportation bottlenecks, and increased lead times for product delivery. As a result, DC operators are often forced to manage more unpredictable inventory flows, complicating stock control and forecasting processes.
These disruptions have made it difficult for companies to maintain the correct stock levels, especially for goods that are sourced internationally. Additionally, with longer lead times, distribution centres must contend with the challenge of holding higher levels of inventory for products, tying up valuable storage space and capital.
3. Rising Operational Costs
As operating costs rise—particularly in areas such as manpower, energy, and real estate—distribution centres are feeling increasing pressure to manage their inventories more efficiently. As mentioned above stockpiling excess goods, either due to poor forecasting or supply chain disruptions, can quickly lead to storage issues. If space is not used effectively, distribution centres risk wasting valuable square footage, which results in higher real estate costs.
On top of that, increasing manpower costs add another layer of complexity. If inventory is not managed in a streamlined manner, it can lead to additional handling and non-value adding movement of stock, further driving up costs.
4. Technological Transformation and Integration
Distribution centres have witnessed significant technological advancements, particularly in the areas of automation, robotics, and inventory management systems (IMS). However, many operations still rely on outdated processes and legacy systems that are not integrated with newer technologies. This can lead to inefficiencies in stock tracking, order processing, and reporting.
A lack of real-time visibility into inventory levels makes it difficult for DC managers to optimize storage, order fulfilment, and replenishment processes. Moreover, without an integrated system, discrepancies between inventory recorded in the DC and actual stock levels can result in errors that affect decision-making and customer service.
5. Inventory Visibility and Accuracy
Manually tracking inventory in today’s complex and fast-moving operations can lead to errors, between actual stock and what is recorded in inventory systems. Poor visibility of stock levels can lead to situations where businesses over-order products, resulting in excess stocks, or under-ordering, and ultimately to stockouts and lost sales. These inaccuracies can also impact the efficiency of order picking and packing, which increases the likelihood of errors in fulfilling customer orders and delays in delivery.
In amongst all these challenges are solutions to take control and really enhance your inventory management.
Given the complexities of modern inventory management, companies are advised to adopt a range of strategies and technologies to overcome these challenges. Here are several potential solutions that can help streamline inventory management processes and drive operational efficiency:
1. Implementing Warehouse Management Systems (WMS)
A Warehouse Management System (WMS) is essential to track and manage inventory in real time. A WMS enables distribution centres to optimize storage, streamline order picking, and improve the accuracy of stock levels. By integrating barcode scanning, location management, and automated reporting, WMS systems provide DC operators with complete visibility over their inventory, allowing informed decisions on restocking, picking, and shipping.
Modern WMS systems are often cloud-based, offering greater flexibility and the ability to connect with other supply chain management tools that utilise AI and machine learning. These allow for more accurate forecasting and demand planning, which helps reduce instances of stockouts or overstocking.
For example, many WMS systems provide features like dynamic slotting, which automatically adjusts the placement of products based on factors such as demand, size, and weight. This feature allows distribution centres to continuously optimize their storage space and reduce inefficiencies caused by poor inventory organization.
2. Using Predictive Analytics and Demand Forecasting
Predictive analytics can help distribution centres anticipate demand fluctuations and optimize inventory levels accordingly. By leveraging historical data, market trends, and real-time insights, AI driven predictive models can provide forecasts on how much of each product will be needed over a given time frame with much greater accuracy than we have experienced previously.
For example, predictive analytics can help DC’s plan for seasonal spikes in demand or anticipate changes in customer preferences. This allows businesses to reduce excess inventory while ensuring they have enough stock to meet customer needs, ultimately improving cash flow and reducing the need for storage space.
Advanced analytics tools can also help businesses identify slow-moving products and determine whether to discount, relocate, or discontinue them, which helps prevent stockpiling and overstocking.
3. Embracing Automation and Robotics
Automation and robotics are transforming the way distribution centres manage inventory. Automated systems like Automated Guided Vehicles (AGVs), robotic arms, and conveyor belts can help streamline the process of receiving, storing, and retrieving goods. These systems can dramatically reduce the amount of time spent on manual handling of inventory, improving accuracy and reducing manpower costs.
Robotic systems, such as collaborative robots (cobots), can assist workers in picking and packing products, improving throughput and reducing human error. In addition, automation can help with stock rotation, ensuring that older products are sold first, which reduces the chances of obsolescence and waste.
4. Real-Time Inventory Tracking and Visibility
To combat inventory discrepancies and improve operational accuracy, distribution centres must have real-time tracking of stock levels. This can be achieved through a combination of IoT-enabled devices, barcode scanning, and continuous inventory checking solutions. Real-time visibility into inventory allows managers to make more informed decisions regarding reordering, stock rotation, and order picking.
With accurate, real-time data, distribution centres can minimize errors, reduce the time spent on manual stocktaking, and provide customers with more accurate delivery windows. It also ensures that stock levels are continuously updated, preventing situations where orders are promised for items that are out of stock.
Conclusion
Inventory management is one of the most critical aspects of distribution centre operations, and in today’s rapidly changing landscape, it has become more complex than ever before. Challenges posed by increased e-commerce demand, supply chain disruptions, rising operational costs, and technological transformation must be addressed. With the right strategies and technologies in place, companies can overcome these challenges and optimize their inventory management processes.
From implementing advanced Warehouse Management Systems to using predictive analytics and automation, the solutions to improve inventory control are diverse and impactful. By adopting a combination of these solutions, DC operators can enhance efficiency, reduce costs, and ultimately deliver better service to customers in an increasingly competitive marketplace.
Beyond Darwin can support you through these transformations, reach out via beyonddarwin.co.uk