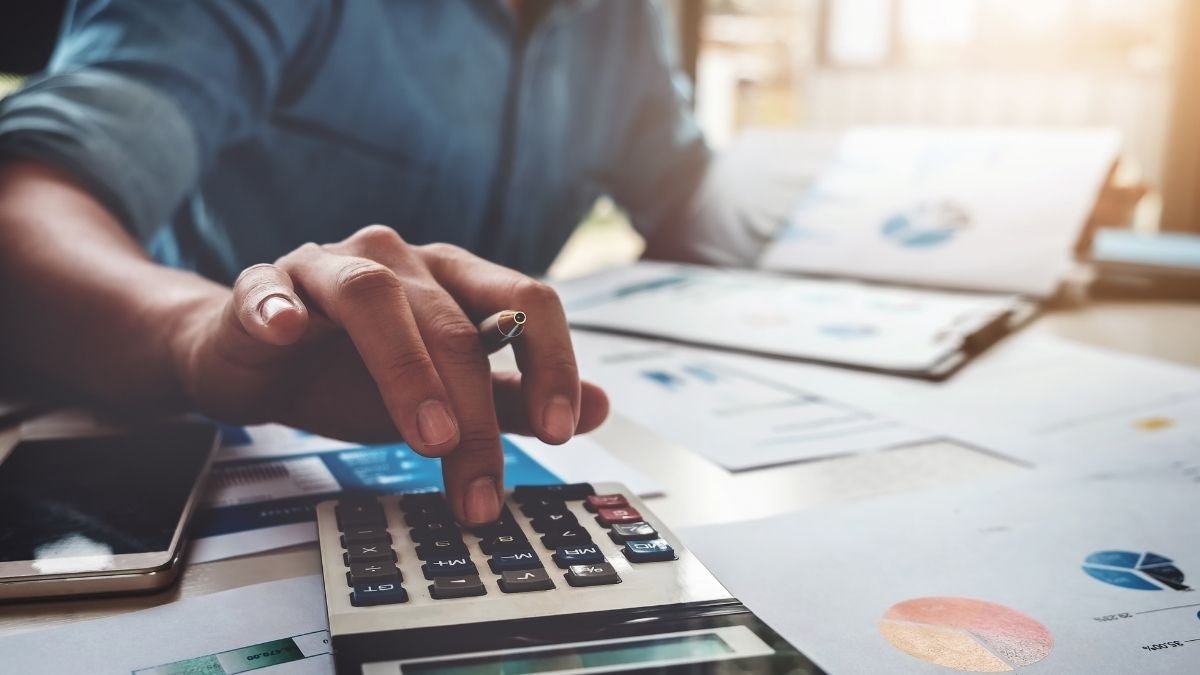
Rising Operational
Costs
UK distribution centres (DC’s) are a cornerstone of the nation’s logistics and supply chain infrastructure.
As the demand for efficient, fast-paced distribution continues to grow, driven largely by the e-commerce boom, DC operators are grappling with rising operational costs. From increasing energy prices and labour expenses to the challenges posed by automation and compliance, the pressures on distribution centres are mounting. Rising operational costs can significantly affect profitability and competitiveness, pushing businesses to seek innovative solutions that can balance the demand for high service levels with the need for cost efficiency.
This thought leadership piece explores the root causes of rising operational costs in UK distribution centres and offers potential solutions to help businesses adapt to these growing financial challenges.
The key root causes of rising operational costs are:
1. Increased Labour Costs
Labour remains one of the largest expenses in DC operations. With a growing shortage of skilled workers in the UK, many businesses are seeing wages climb as they compete for a limited pool of talent. The logistics sector, which has historically relied on low-wage, manual labour, now finds itself under pressure to offer higher pay and benefits to attract and retain workers.
Moreover, factors like an aging workforce, a reluctance among younger workers to pursue physically demanding roles, and changes to immigration policy post-Brexit have further exacerbated labour shortages. As businesses increase wages to keep up with the competition, the overall cost of labour rises, leading to higher operational costs. Distribution centres are also burdened by increasing turnover rates, which mean more investment in recruitment and training.
2. Energy and Utility Costs
Another major contributor to rising operational costs is the escalation in energy prices. DC’s, particularly large operations, consume significant amounts of energy to power lighting, heating, cooling, and machinery. The UK has seen significant volatility in energy prices in recent years, exacerbated by global energy market fluctuations, the ongoing transition to renewable energy sources, and geopolitical issues.
For distribution centres with large cold storage facilities or those that operate 24/7, energy expenses can constitute a substantial portion of total operating costs. Furthermore, stricter regulations related to sustainability and carbon emissions are pushing distribution centres to adopt more energy-efficient practices or invest in renewable energy solutions, which require significant capital expenditure upfront.
3. Real Estate and Space Constraints
As demand for distribution centres and logistics services grows, particularly in urban areas close to key transportation hubs, real estate prices have increased. Distribution centres are forced to operate in premium locations to meet the expectations of fast delivery times in the e-commerce era, often driving up rental costs and the price of land.
Additionally, rising property costs often lead to smaller distribution centre spaces and a need for more efficient use of space. This can increase operational complexity, as operators must balance the need for space with the demand for high efficiency in inventory management, order fulfilment, and packing.
4. Regulatory Compliance and Sustainability
Distribution centres in the UK face increasing pressure to comply with a variety of regulations, from health and safety standards to environmental legislation. The UK government’s carbon reduction targets have led to stricter energy efficiency standards, prompting DC’s to invest in technologies like LED lighting, automated temperature control systems, and energy-efficient equipment.
Further, operators must address consumer and investor demand for sustainability, which often requires adopting greener practices, such as reducing waste, minimizing carbon footprints, and using more sustainable packaging. These initiatives, while critical to long-term environmental goals, also add to operational costs in the short term due to the need for new equipment, technology, and systems.
5. Technology and Automation Costs
While automation offers long-term operational efficiencies, the upfront investment in technology can significantly increase operational costs in the short term. Automated systems, such as robotic pickers, conveyor belts, and AI-driven warehouse management systems (WMS), can require high initial capital expenditures, although, more are becoming available on a lease basis. Additionally, maintaining these systems, training staff to use them effectively, and ensuring cybersecurity is costly compared to a traditional manual operation.
As the industry embraces digital transformation to improve efficiency and meet customer expectations, these technology costs become an important factor in rising operational expenses.
Despite the many challenges posed by rising operational costs, several strategies can help operators mitigate these challenges and find efficiencies that allow them to remain competitive and profitable.
1. Embrace Automation and Robotics
Robotics, AI, and machine learning can streamline DC operations by automating repetitive tasks, improving inventory management, and reducing human error. Automated guided vehicles (AGVs) can transport goods around the distribution centre without human intervention, while robotic arms can handle sorting, packaging, and palletizing. Although automation can require an upfront investment, the long-term benefits often outweigh the initial costs. Certain elements of these solutions can also be purchased as a lease, reducing the burden of high CAPEX approvals.
By reducing the reliance on manual labour, companies can offset the impact of rising labour costs. Furthermore, automation systems can increase productivity, reduce cycle times, and improve accuracy, all of which can contribute to lowering overall operational expenses.
2. Adopt Energy-Efficient Technologies
As energy costs continue to rise, investing in energy-efficient technologies can provide a long-term return on investment. Distribution centres can implement energy-saving solutions, such as LED lighting, automated lighting systems, and energy-efficient HVAC systems. Additionally, investing in renewable energy sources, like solar panels, can help offset rising electricity prices while contributing to sustainability goals.
DC operators can also explore energy-efficient building designs, such as high-insulation materials and optimized layouts that reduce the need for energy-intensive climate control. Monitoring energy usage with IoT-enabled systems allows businesses to track and optimize energy consumption in real-time, leading to reduced waste and lower bills.
3. Optimize Space Utilization
Effective space management is critical in controlling rising real estate costs. Implementing advanced warehouse management systems (WMS) can help optimize space utilization by allowing operators to track inventory in real-time and identify areas for more efficient storage. With better data, distribution centres can increase storage density, minimize wasted space, and optimise layouts for improved efficiency.
In addition, using vertical storage solutions like mezzanine floors or high-bay racking systems can maximize available space without the need for additional square footage. Multi-level shelving systems, combined with automated systems, can further increase capacity and reduce the need for additional distribution centres or expansion.
4. Leverage Data and Advanced Analytics
Data-driven decision-making is crucial in improving efficiency and controlling costs. By using real-time data from WMS, businesses can monitor inventory levels, track order fulfillment rates, and identify bottlenecks or inefficiencies. Predictive analytics can also help anticipate demand surges, enabling distribution centres to better plan staffing levels, inventory needs and layouts.
Moreover, advanced analytics can highlight areas where operational processes can be streamlined, helping operational leaders make data-backed decisions that reduce costs and improve productivity.
5. Outsource Non-Core Activities
For some distribution centre operators, outsourcing non-core functions, such as transportation, maintenance, or packaging, can help reduce operational costs. By leveraging third-party logistics providers or outsourcing certain tasks, operators can focus on their core competencies and take advantage of the expertise and economies of scale offered by external partners.
Outsourcing also helps mitigate fluctuations in demand, allowing businesses to scale their operations more flexibly without committing to fixed costs or long-term investments in additional infrastructure.
6. Workforce Training and Retention
Investing in workforce training and development can also help mitigate rising labour costs. By upskilling current employees in new technologies and processes, distribution centres can enhance productivity and reduce the reliance on costly recruitment and turnover. Offering a clear career progression path and improving employee retention can further reduce recruitment costs and improve long-term workforce stability.
Additionally, introducing flexible working arrangements, where possible, can help attract and retain employees, particularly in the face of labour shortages and increasing competition for talent.
Managing your headcount by introducing automation and outsourcing non-core activities means investing in your core team is achievable, and to maintain stability, essential.
Conclusion
Rising operational costs in UK distribution centres present significant challenges for operators, but with the right strategies in place, these costs can be managed effectively. By embracing automation, improving energy efficiency, optimizing space utilization, leveraging data, and investing in workforce training, businesses can reduce costs while improving productivity and service levels.
The key to addressing these rising costs lies in balancing short-term investments with long-term operational improvements. By making strategic decisions today, businesses can not only manage rising costs but also position themselves for success in an increasingly competitive and rapidly evolving logistics market.
Beyond Darwin can guide you on this journey, contact us at Beyond Darwin
For more contact me via the button below.