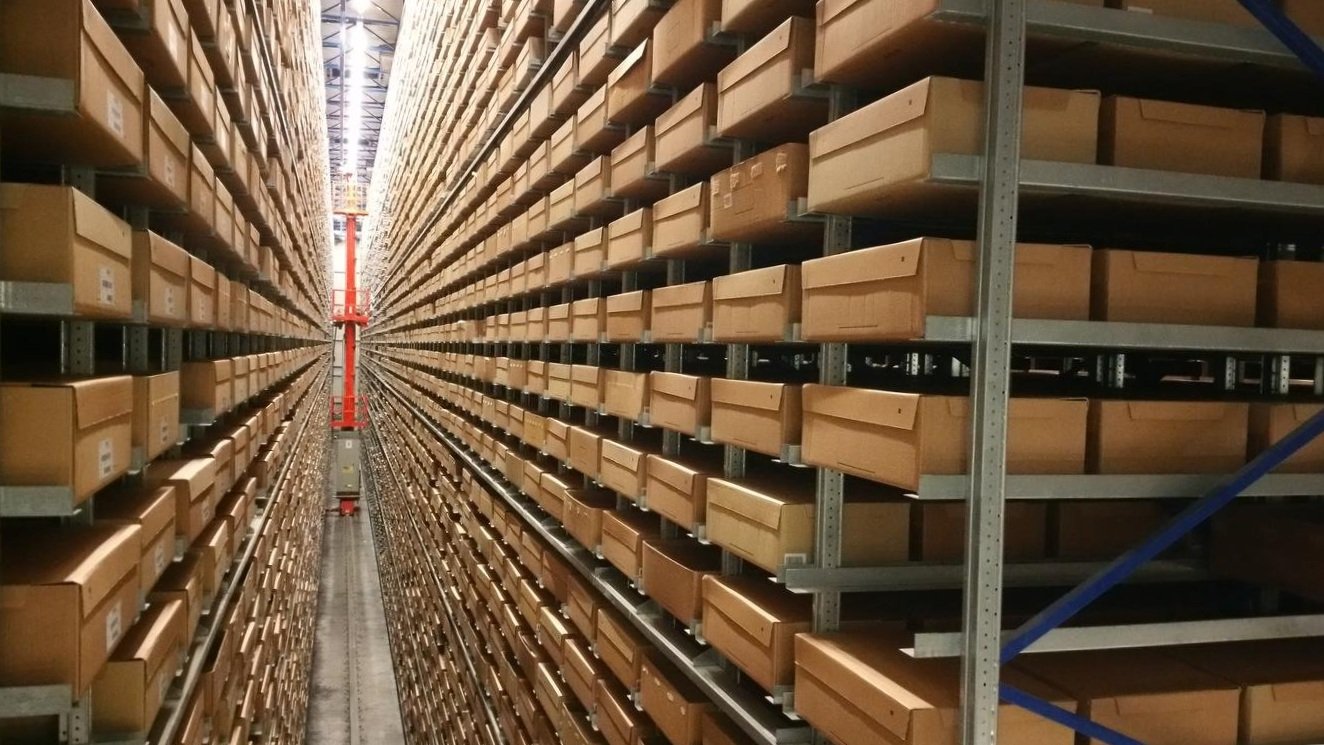
Achieving Space
Optimisation
In the ever-evolving world of logistics, distribution centres (DCs) are at the heart of the supply chain, serving as the critical hub between manufacturing and end consumers.
However, as demand for rapid fulfilment grows and supply chain disruptions increase, space has become increasingly scarce. Making space optimization one of the most pressing challenges for businesses. From rising real estate costs to the increased demand for e-commerce fulfilment, distribution centre managers are under immense pressure to maximize every square foot of their facilities while maintaining efficiency and minimising costs.
The challenge of space optimisation is not just about squeezing more goods into existing areas; it’s about ensuring that the DC is configured in such a way that both physical space and manpower are used as efficiently as possible. In this article I will explore the current space optimisation challenges being faced and consider potential solutions to address these issues.
Firstly, what drives the growing challenge of space optimisation in distribution centres?
1. Rising Real Estate Costs
The demand for distribution centre space in the UK, particularly in urban areas and locations close to major transport hubs, has skyrocketed in recent years. The explosion of e-commerce has led to an increase in the volume of goods moving through distribution centres, whilst ongoing international supply chain disruptions (Geopolitics, war, etc) are driving up the demand for local inventory. These trends are pusing the need for more and more space. However, the scarcity of available land and rising property prices in key logistics locations have made acquiring additional distribution centre space prohibitively expensive.
In areas like the Southeast of England, real estate prices are among the highest in Europe, forcing many companies to either settle for smaller spaces or operate in less-than-ideal locations. So, maximizing storage capacity within limited spaces without sacrificing operational efficiency is critical to all DC operations.
2. E-Commerce and Inventory Complexity
The boom in online retail has dramatically shifted the way distribution centres function. Today’s consumers expect quick, often same-day, delivery services, creating pressure on DCs to handle a greater number of smaller orders, often with diverse inventories. Unlike traditional wholesale operations where items are large and relatively few, e-commerce involves handling a vast array of smaller, more diverse products.
This shift introduces additional complexity when it comes to organizing inventory in a way that allows for fast picking, packing, and shipping. When managing large numbers of stock-keeping units (SKUs) in smaller volumes, distribution centres can quickly become overcrowded, making space utilization and inventory flow more difficult to manage. Add in high numbers of returns and you have a perfect storm brewing.
3. Inventory Management and Order Fulfilment
In a traditional DCs, the process of receiving, storing, picking, and shipping goods follows a straightforward linear path. However, modern operations, particularly those that deal with e-commerce fulfillment, need to accommodate a continuous, dynamic flow of inventory and orders. This complexity makes it even harder to optimize space effectively.
For instance, many DCs struggle with managing how to layout and store a mix of fast moving goods and slow moving items. Poor inventory management can result in underutilized storage space for less popular products and overcrowding in sections where more popular products are stored. This imbalance creates inefficiencies that further reduce the distribution centre’s overall effectiveness.
4. Labor Shortages and Staffing Costs
Labour shortages are a thorn in the side of distribution centres, and they impact space optimization efforts. The lack of sufficient skilled workers can reduce the speed and accuracy with which DCs are able to operate. This can result in poorly organized spaces, inefficient inventory flows, and ultimately wasted space.
Additionally, manpower costs are rising due to the competition for staff, particularly considering post-Brexit immigration policies, which have limited the influx of workers from the EU. With this back story, companies are looking for ways to optimize the use of their workforce and physical space simultaneously, making it a more intricate challenge.
These are significant challenges, however, there are solutions that can support space optimization.
Given the complexity of space optimization challenges, DC operators must explore a range of innovative solutions that balance efficiency, cost, and flexibility. Below are several strategies that can help:
1. Utilizing Vertical Space
One of the most straightforward solutions to space constraints is to leverage vertical space. Many distribution centres still operate in a way that maximizes only the horizontal space, leaving the vertical dimension largely untapped. By installing taller racking systems or mezzanine floors, DCs can significantly increase their storage capacity without having to expand their physical footprint.
Using automated vertical storage systems such as vertical lift modules (VLMs) or high-bay racking, further optimized use of vertical space can be achieved. Helping to maximize storage density and improve inventory flow.
2. Implementing Automated Storage and Retrieval Systems (ASRS)
Automated Storage and Retrieval Systems (ASRS) are a popular solution for space optimization in modern distribution centres. These systems use robotic shuttles or automated cranes to retrieve and store products efficiently. By reducing the need for manual handling and optimizing storage density, ASRS can maximize the use of vertical and horizontal space within a distribution centre.
ASRS systems can also help reduce picking times and improve accuracy by automatically bringing items to workers or automated pick stations. For high-volume, fast-paced environments such as e-commerce, where small orders need to be picked quickly, ASRS is an effective way to increase throughput while reducing the footprint of the distribution centre.
3. Warehouse Management System (WMS) Optimization
A robust and functionally rich Warehouse Management System (WMS) is essential for improving space utilization. These systems track inventory in real time, helping DC managers make data-driven decisions about where products should be stored and how to optimize picking routes.
Advanced WMS platforms also allow for dynamic slotting, where products can be moved within the distribution centre as demand fluctuates. For example, seasonal items can be moved to more accessible locations during peak demand periods, and less frequently ordered goods can be stored in more remote areas of the distribution centre. AI enabled planning systems can further support this optimisation.
It is also important for WMS systems to be compatible with Warehouse Control Systems (WCS) and Warehouse Execution Systems (WES). These complimentary systems are used by automated and robotic solutions to optimise service and efficiency.
4. Racking and Shelving Solutions
Something as simple as the right type of shelving and racking can be game changing in how space is utilized. Many distribution centres use basic racking systems, but there are numerous innovative racking options that maximize the use of space. For example, for less complex operations, push-back racking allows for dense storage while maintaining easy access to products. Likewise, drive-in racking, where forklifts drive into the racks, offers high-density storage for bulk goods that do not need to be accessed frequently.
Mobile shelving is another space-saving solution, which involves moving shelving units along tracks, creating adjustable aisles based on need. This system works particularly well in smaller spaces or when flexibility is required to accommodate varying inventory levels.
5. Cross-Docking
The ultimate space optimisation solution is to not store the products in the DC at all. Cross-docking can help optimise space and improve inventory flow by receiving products and immediately transferring them to outbound shipping docks, without touching any storage. This process minimizes the amount of time inventory spends in the DC, freeing up valuable space for incoming goods.
Cross-docking is particularly effective for time-sensitive products and perishable goods and is commonly used in retail, where fast inventory turnover is essential. It allows DCs to function more like transit hubs, improving space utilization. However, you need to have confidence in your suppliers, failure to deliver hits customer availability immediately, therefore it requires careful consideration.
The benefits of cross docking are significant, but so are the risks.
6. Flexible Distribution centres and Shared Space Models
With the increasing costs of leasing distribution centre space, another emerging trend is the use of flexible distribution centre solutions. Shared space or multi-client distribution centres allow businesses to share storage space, reducing overhead costs and maximizing efficiency. The use of automated storage and retrieval systems (ASRS) is a great enabler for effective multi-client DCs
These models also allow for scalability. During peak periods, businesses can scale up their storage needs without committing to long-term leases or capital investments. This flexibility can be particularly useful for smaller businesses or companies with fluctuating demand, such as seasonal retailers.
Flexible space, if contracted correctly, can provide that vital space optimization. To be successful, it requires effective forward planning to ensure you secure your seasonal space before your competitors.
Conclusion
Space optimisation is one of the most significant challenges facing distribution centres. By adopting a combination of innovative technologies, optimizing storage systems, and leveraging flexible models, companies can find solutions that maximize space efficiency without compromising on service levels or operational performance.
The key to effective space optimization lies in understanding the unique needs of each operation and implementing strategies that combine technology, layout design, and workforce management. As operations continue to evolve, businesses that embrace space optimisation solutions will position themselves for greater operational success, ultimately improving efficiency, reducing costs, and enhancing customer satisfaction.
For support and guidance through the journey to optimised storage, click the button below to set up a call.