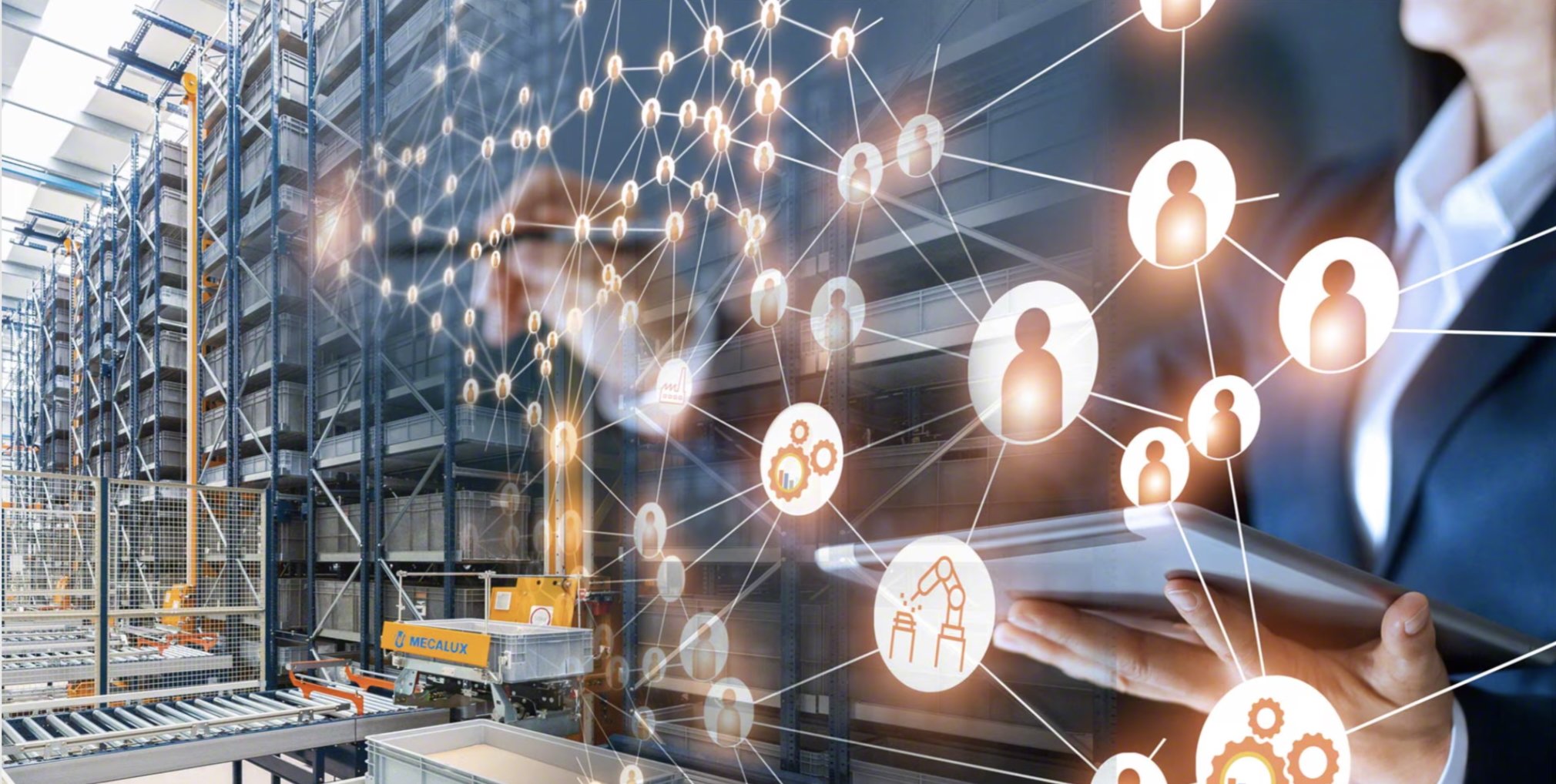
Integrating Technology
Seamlessly
In today’s fast-paced and increasingly competitive landscape, UK distribution centres (DC’s) are experiencing a rapid technological transformation. From automation and robotics to advanced warehouse management systems (WMS) and artificial intelligence (AI), the rise of technology in the logistics industry has the potential to revolutionize operations. However, integrating these advanced technologies presents a host of challenges for businesses of all sizes.
As the demand for faster delivery times, increased efficiency, and real-time data grows, operators must embrace the digital revolution to stay competitive. But while technology offers vast potential for improvement, the integration of these systems comes with its own set of hurdles, including system compatibility, cost, and resistance to change. To successfully harness the power of new technologies, it’s essential for operators to understand the challenges they face and explore the solutions that can drive seamless integration.
Warehousing has always been pivotal to the supply chain, but the rapid growth of e-commerce, the push for faster deliveries, and the increasing demand for supply chain transparency have placed new pressures on DCs. In this dynamic environment, distribution centres are tasked with managing larger quantities of stock, handling more diverse inventories, and processing a higher volume of orders—all within shorter timeframes.
Technology offers a clear solution to these challenges. Automation tools, such as Automated Guided Vehicles (AGVs), robotics, and conveyor systems, can reduce manual labor and increase order picking speed. Warehouse Management Systems (WMS) and Inventory Management Systems (IMS) provide real-time data on stock levels, optimizing inventory management and reducing stockouts or overstocking. Moreover, the integration of Artificial Intelligence (AI) and machine learning can enhance forecasting accuracy, planning and improve decision-making.
However, integrating these technologies into existing systems is not always straightforward. The complexity of these integrations, along with several operational challenges, creates barriers that DC operators must overcome to fully capitalize on technological advancements.
Let’s breakdown the key obstacles when it comes to integrating technology into a modern distribution centre.
1. System Compatibility and Integration Issues
One of the primary challenges of technology integration in DC’s is ensuring that new systems work seamlessly with existing infrastructure. Many distribution centres operate with legacy systems that were not designed to communicate with modern technologies. For example, traditional inventory systems may not be able to sync with newer WMS or AI-driven analytics tools, which can lead to data silos and operational inefficiencies.
The integration of new technologies requires a high level of interoperability between various platforms, software, and devices. The lack of compatibility between legacy systems and newer technologies can lead to delays, additional costs, and disruptions in operations.
2. High Upfront Costs and ROI Uncertainty
Another significant barrier to technology integration is the perceived high initial investment required for implementing advanced systems and automation technologies. While the long-term benefits of technology, such as increased efficiency and reduced labor costs, are well-documented, many operators are hesitant to make such substantial upfront investments, particularly in a challenging economic environment.
For small and mid-sized operators, the cost of purchasing and implementing automation systems, AI software, or advanced WMS can be prohibitively expensive. Moreover, the return on investment (ROI) can be difficult to measure, especially if the technology is not integrated smoothly or if it takes time for the system to deliver tangible benefits.
Given the uncertainty surrounding the ROI of technology investments, distribution centre operators may be reluctant to adopt new technologies without a clear understanding of the financial benefits or without sufficient capital to fund the necessary upgrades.
3. Resistance to Change
In many distribution centre environments, there is often resistance to adopting new technologies, particularly among staff who have been accustomed to traditional ways of working. This resistance can stem from fear of job displacement, lack of understanding of the new systems, a low level of trust in management, or concerns about the complexity of integrating new technologies into daily workflows.
Distribution centre workers and managers may feel apprehensive about the shift from manual processes to automated ones, especially if they believe their skills may become obsolete or if they are uncertain about how to operate new systems. This cultural resistance to change can slow down the adoption of new technologies and hinder their effective integration.
4. Data Management and Security Concerns
As distribution centres increasingly rely on digital solutions, the amount of data generated by technologies such as WMS, scanning, sensors, and AI-powered analytics tools is growing exponentially. This data holds valuable insights into inventory levels, order trends, and customer behaviours, but managing and securing this data becomes a significant challenge.
Without the proper infrastructure to manage and protect this data, distribution centres risk data breaches, theft, or loss, which could result in operational disruptions, loss of customer trust, or legal consequences. Furthermore, data overload can make it difficult for operators to extract actionable insights in a timely manner, leading to inefficiencies and missed opportunities.
5. Scalability Issues
As distribution centres continue to evolve in response to changing customer demands and supply chain disruptions, the scalability of new technologies becomes a critical consideration. Many technologies, such as automation systems, are not always easily scalable and may require significant investments or infrastructure changes to grow with the business.
Distribution centre operators need solutions that can adapt to fluctuating demand, changing inventory volumes, and varying order sizes. Systems that are too rigid or difficult to scale can limit the long-term success of technology adoption and increase operational costs as the DC expands or faces seasonal demand spikes.
Despite these challenges, there are several potential solutions that can help successfully integrate new technologies and ensure long-term success.
1. Adopting Modular and Scalable Technologies
To address the issue of scalability, DC operators should consider investing in modular and scalable technologies. These systems are designed to grow with the business, enabling operators to add new capabilities or expand existing systems without major disruptions.
For example, the latest automated picking solutions don’t require significant amounts of expensive, fixed assets like conveyor, or sortation. It is possible to adapt current operations to utilise robotics to work with your workforce more effectively.
This means that solutions can be introduced in a more simplistic manner. If proven to be successful the level of sophistication can then be increased in modular fashion to ensure the minimal disruption, and to manage the investment risk.
2. Prioritizing Employee Training and Change Management
To overcome resistance to change, DC operators must focus on employee training and change management. By investing in training programs and demonstrating the benefits of new technologies, businesses can alleviate fears and build confidence in staff. DC workers should be equipped with the skills they need to operate new systems and understand why these changes are necessary / beneficial, and how these technologies will improve their workflows, rather than replace their roles.
Moreover, implementing a clear change management strategy can help facilitate smoother transitions. Involving employees in the decision-making process, communicating the reasons for technology adoption, and addressing concerns early on can help minimize resistance and increase buy-in from the workforce.
Change management cannot be underestimated, it is critical in obtaining adoption to change.
3. Collaborating with Expertise
Given the complexity of technology integration, collaborating with experienced personnel is crucial. Distribution centre operators should ideally seek out independent consultants with a proven track record to ensure that the operators’ true requirements can be met by the vendors and system integrators tasked with designing and implementing these advanced solutions. It is unrealistic to expect operations teams to be able to navigate these complex solutions without support.
These experienced consultants can offer valuable, and most importantly, impartial expertise in system integration, ensuring that different technologies, such as WMS, robotics, and AI tools, work together seamlessly. They can also ensure that the right ongoing support and training is put in place to help operators to continue to optimize their systems and maximize ROI.
4. Ensuring Data Security and Compliance
As data security becomes more critical, distribution centre operators must invest in robust cybersecurity measures and comply with relevant data protection regulations, such as the General Data Protection Regulation (GDPR) in the UK and EU. Implementing encrypted data storage, regular security audits, and access controls can help safeguard sensitive information and reduce the risk of breaches.
Additionally, leveraging advanced analytics tools can help operators make sense of the vast amounts of data generated by modern systems, ensuring that valuable insights are easily accessible and actionable.
5. Implementing Phased Technology Rollouts
To minimize disruption during the integration process, distribution centres should consider implementing technology upgrades in phases. By introducing new systems gradually, operators can mitigate risks, troubleshoot problems, and make necessary adjustments before fully committing to a complete rollout.
For example, distribution centres could start by automating specific tasks, such as order picking or inventory tracking, before expanding automation across the entire operation. This phased approach allows operators to gain experience with new technologies while maintaining control over the integration process.
6. Non-CAPEX implementations
Managing the difficulty of the high investment in new systems and technology can be achieved through following the above modular approach to phase the cost of investment. It is also possible to, in some circumstances, to remove the CAPEX altogether. Many companies now provide leasing options that mean no upfront investment, or a reduced upfront investment, simply committing to a monthly charge across a 3 to 5 year period.
This also supports the management of risk that your business requirements can change. If they do, you have the option to replace / amend the solution once the lease is completed.
These options can reduce the barriers to implementing technology considerably.
Conclusion
The integration of new technologies in distribution centres holds immense potential to increase efficiency, reduce costs, and enhance customer satisfaction. However, the challenges of system compatibility, high costs, resistance to change, and data management require careful planning and strategy.
By adopting modular, scalable technologies, prioritizing employee training, collaborating with experienced consultants, ensuring robust data security, and rolling out systems in phases, DC operators can overcome these challenges and successfully integrate new technologies into their operations, with the cost of investment under control.
In an increasingly competitive and fast-paced market, embracing technology is no longer optional—it is essential. Those who can successfully navigate the complexities of technology integration will be well-positioned to thrive in the future of distribution centre operations and supply chain management.
Beyond Darwin can provide experienced, independent, support to ensure your technology integration is seamless. Reach out at beyonddarwin.co.uk